Portfolio
TPM
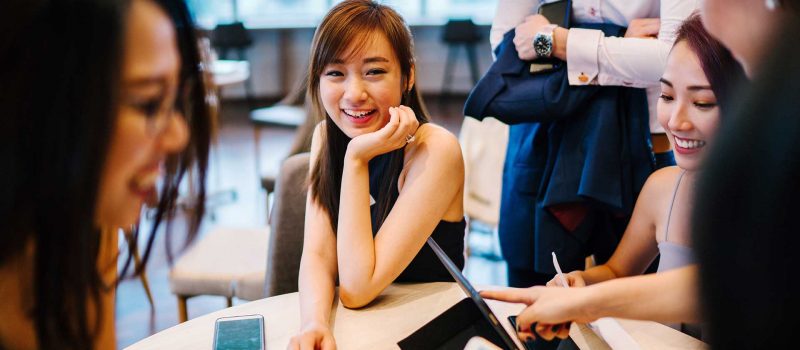
Descripción
Uno de los principales pilares del Mantenimiento Productivo Total (TPM) es el de las Mejoras Enfocadas o, mejor dicho, kobetsu kaizen (個別改善). Se trata, básicamente, de una metodología cuyo fin principal es el de reducir pérdidas en los procesos. A través de la formación de grupos multidisciplinarios interrelacionados, se establece una manera sistemática de aplicar mejoras que apunten a reducir o eliminar por completo estas pérdidas.
Subtemas
Definición:
Uno de los principales pilares del Mantenimiento Productivo Total (TPM) es el de las Mejoras Enfocadas o, mejor dicho, kobetsu kaizen (????). Se trata, básicamente, de una metodología cuyo fin principal es el de reducir pérdidas en los procesos. A través de la formación de grupos multidisciplinarios interrelacionados, se establece una manera sistemática de aplicar mejoras que apunten a reducir o eliminar por completo estas pérdidas.
Beneficios:
Uno de los principales pilares del Mantenimiento Productivo Total (TPM) es el de las Mejoras Enfocadas o, mejor dicho, kobetsu kaizen (????). Se trata, básicamente, de una metodología cuyo fin principal es el de reducir pérdidas en los procesos. A través de la formación de grupos multidisciplinarios interrelacionados, se establece una manera sistemática de aplicar mejoras que apunten a reducir o eliminar por completo estas pérdidas.
Beneficios:
- Eliminar radicalmente las causas de las pérdidas crónicas Mejorar el conocimiento de los procesos mediante el análisis y solución de problemas en forma continua
- Involucrar al todo el personal de la empresa en acciones de mejora individual y grupal Mejorar la eficiencia del trabajo humano
Definición:
El enfoque de Mantenimiento Productivo (TPM) está acercando a los fabricantes a hacer esto realidad. Ya sea que haya experimentado con TPM en el pasado o que sea relativamente nuevo en el concepto, vale la pena entender lo que se puede obtener de él. TPM es una filosofía de manufactura esbelta que se centra en lograr una roducción casi perfecta. Los objetivos de TPM son altos: sin fallas, sin pequeñas paradas o funcionamiento lento, sin defectos y sin accidentes. Enfatiza el mantenimiento proactivo y preventivo para maximizar la vida útil y la productividad de los equipos. Y lo hace al capacitar a todos los empleados para que asuman la responsabilidad de dicho equipo
Beneficios:
Cuando se crean las iniciativas de TPM hay que tener bien claro cuáles son sus pilares y definir los roadmaps necesarios para llegar a tener implementada una de las herramientas más poderosas de Lean Manufacturing, ya que el impacto en el OEE es directamente proporcional a la implementación dedicada de cero paros por averías y cero defectos.
El enfoque de Mantenimiento Productivo (TPM) está acercando a los fabricantes a hacer esto realidad. Ya sea que haya experimentado con TPM en el pasado o que sea relativamente nuevo en el concepto, vale la pena entender lo que se puede obtener de él. TPM es una filosofía de manufactura esbelta que se centra en lograr una roducción casi perfecta. Los objetivos de TPM son altos: sin fallas, sin pequeñas paradas o funcionamiento lento, sin defectos y sin accidentes. Enfatiza el mantenimiento proactivo y preventivo para maximizar la vida útil y la productividad de los equipos. Y lo hace al capacitar a todos los empleados para que asuman la responsabilidad de dicho equipo
Beneficios:
Cuando se crean las iniciativas de TPM hay que tener bien claro cuáles son sus pilares y definir los roadmaps necesarios para llegar a tener implementada una de las herramientas más poderosas de Lean Manufacturing, ya que el impacto en el OEE es directamente proporcional a la implementación dedicada de cero paros por averías y cero defectos.
- Menos tiempo de mantenimiento no planificado
- Un ambiente de trabajo más seguro.
- Mayor calidad de salida de los procesos
- Impacto comprobado
Definición:
TPM contribuye al desarrollo de una cultura de calidad y productividad, proporciona a su personal la oportunidad de realizar el mantenimiento autónomo y conservar en óptimas condiciones de funcionamiento su máquina o equipo La utilidad del TPM es universal ya que puede aplicarse en cualquier tipo de empresa no importando el tipo o giro de la misma. El TPM lo puede realizar cualquier operador sin necesidad de contar con algún grado de estudios o especialización."
Beneficios:
"El Mantenimiento Productivo Total ayuda a prestar atención inmediata a algunos problemas menores antes de que el problema se agrave. Reducción de la mano de obra total. Reducción de retrasos y pérdidas de tiempo de inactividad al reducir las averías y fallas del equipo y al reducir los tiempos de ajuste y configuración, por ejemplo, configuración de guías, cambio de herramientas y matrices, etc. Reducción de las pérdidas de velocidad, mediante la reducción de los tiempos de inactividad y las paradas menores causadas por la interfaz de mantenimiento del operador y mediante la reducción de las pérdidas debido a una velocidad más baja y una tasa de salida inferior a la diseñada. Reducción de pérdidas por defectos y pérdidas de rendimiento al mejorar la producción de calidad y por una estabilización más rápida de la producción. TPM garantiza mejores y más medidas de ahorro de energía y también una mayor seguridad de los hombres y las máquinas, ya que todas las personas interesadas conocen el equipo y esos dispositivos.TPM garantiza una disponibilidad más rápida de repuestos de calidad, materiales y otros servicios, ya que las personas responsables de estos también están más involucradas y conectadas con el mantenimiento y mantenimiento de los equipos
TPM contribuye al desarrollo de una cultura de calidad y productividad, proporciona a su personal la oportunidad de realizar el mantenimiento autónomo y conservar en óptimas condiciones de funcionamiento su máquina o equipo La utilidad del TPM es universal ya que puede aplicarse en cualquier tipo de empresa no importando el tipo o giro de la misma. El TPM lo puede realizar cualquier operador sin necesidad de contar con algún grado de estudios o especialización."
Beneficios:
"El Mantenimiento Productivo Total ayuda a prestar atención inmediata a algunos problemas menores antes de que el problema se agrave. Reducción de la mano de obra total. Reducción de retrasos y pérdidas de tiempo de inactividad al reducir las averías y fallas del equipo y al reducir los tiempos de ajuste y configuración, por ejemplo, configuración de guías, cambio de herramientas y matrices, etc. Reducción de las pérdidas de velocidad, mediante la reducción de los tiempos de inactividad y las paradas menores causadas por la interfaz de mantenimiento del operador y mediante la reducción de las pérdidas debido a una velocidad más baja y una tasa de salida inferior a la diseñada. Reducción de pérdidas por defectos y pérdidas de rendimiento al mejorar la producción de calidad y por una estabilización más rápida de la producción. TPM garantiza mejores y más medidas de ahorro de energía y también una mayor seguridad de los hombres y las máquinas, ya que todas las personas interesadas conocen el equipo y esos dispositivos.TPM garantiza una disponibilidad más rápida de repuestos de calidad, materiales y otros servicios, ya que las personas responsables de estos también están más involucradas y conectadas con el mantenimiento y mantenimiento de los equipos
Definición:
El mantenimiento autónomo es el primer paso en el proceso de implementación del Mantenimiento Productivo Total. Representa un enfoque de mantenimiento donde los operadores de máquinas toman la responsabilidad de las tareas básicas de mantenimiento lejos del personal de mantenimiento. Mantenimiento autónomo en TPM En la práctica, esto significa que los operadores de la máquina realizan acciones como controles de seguridad, limpieza y lubricación, lo que brinda a los técnicos de mantenimiento la libertad de concentrarse en tareas de mantenimiento más complejas. Cuando se implementa correctamente, el mantenimiento autónomo puede traer muchos beneficios adicionales."
Beneficios:
Aunque algunos altos ejecutivos estarían muy entusiasmados al ver esto, el mantenimiento autónomo no es una nueva estrategia de mantenimiento en la que los robots conducen y diagnostican y realizan instantáneamente el trabajo de mantenimiento necesario. Por el contrario, el mantenimiento autónomo amplía las responsabilidades de mantenimiento del equipo a los operadores de máquinas y, a menudo, requiere un cambio significativo en la mentalidad de la organización para una implementación exitosa. Asegurar que el equipo se limpie y lubrique adecuadamente. Notar problemas antes de que conduzcan a fallas críticas Liberación de personal de mantenimiento para tareas de nivel superior Mejora de la participación de los empleados y el sentido de relevancia en el panorama general Mejora de la seguridad general"
El mantenimiento autónomo es el primer paso en el proceso de implementación del Mantenimiento Productivo Total. Representa un enfoque de mantenimiento donde los operadores de máquinas toman la responsabilidad de las tareas básicas de mantenimiento lejos del personal de mantenimiento. Mantenimiento autónomo en TPM En la práctica, esto significa que los operadores de la máquina realizan acciones como controles de seguridad, limpieza y lubricación, lo que brinda a los técnicos de mantenimiento la libertad de concentrarse en tareas de mantenimiento más complejas. Cuando se implementa correctamente, el mantenimiento autónomo puede traer muchos beneficios adicionales."
Beneficios:
Aunque algunos altos ejecutivos estarían muy entusiasmados al ver esto, el mantenimiento autónomo no es una nueva estrategia de mantenimiento en la que los robots conducen y diagnostican y realizan instantáneamente el trabajo de mantenimiento necesario. Por el contrario, el mantenimiento autónomo amplía las responsabilidades de mantenimiento del equipo a los operadores de máquinas y, a menudo, requiere un cambio significativo en la mentalidad de la organización para una implementación exitosa. Asegurar que el equipo se limpie y lubrique adecuadamente. Notar problemas antes de que conduzcan a fallas críticas Liberación de personal de mantenimiento para tareas de nivel superior Mejora de la participación de los empleados y el sentido de relevancia en el panorama general Mejora de la seguridad general"
Definición:
"El Mantenimiento Centrado en Confiabilidad (RCM) es un proceso de mantenimiento personalizado determinado a través del análisis de modos de falla potenciales y su impacto en el rendimiento del sistema. Iniciado por la industria de las aerolíneas, el mantenimiento centrado en la confiabilidad abarca el mantenimiento reactivo, preventivo y predictivo (basado en la condición), así como los procesos de búsqueda de fallas para detectar modos de falla ocultos o latentes. Al estudiar las relaciones de causa y efecto junto con la probabilidad y el resultado de cada falla, las tareas de mantenimiento pueden priorizarse de manera rentable en función de la seguridad y la importancia de cada activo para la operación general."
Beneficios:
La implementación exitosa de RCM puede conducir a una mejora en el rendimiento general de los costos, menor tiempo de inactividad y una mayor comprensión del perfil de riesgo general de la organización. Al implementar un método coherente y estructurado para decidir si se deben usar estrategias predictivas, preventivas o de fracaso, el mantenimiento centrado en la confiabilidad puede eliminar las conjeturas y el debate de estas decisiones importantes. Con una perspectiva organizacional de alto nivel, a menudo se pueden evitar prácticas de mantenimiento derrochadoras del tipo ""cortador de galletas"". Los principios de mantenimiento centrados en la confiabilidad también se pueden usar para extender la vida útil del equipo basando las decisiones de reemplazo en la condición del equipo en lugar de los ciclos de vida predeterminados. A medida que se eviten más fallas, los gastos operativos se beneficiarán de reparaciones reducidas, revisiones y tiempos de inactividad. La seguridad y la protección son las consideraciones más importantes de RCM, por lo que se evitan daños a la propiedad y / o al medio ambiente mientras se mejora la participación y la satisfacción de los empleados. El mantenimiento centrado en la confiabilidad es potencialmente la estrategia de mantenimiento general más eficiente porque los procesos de mantenimiento más complejos solo se aplican cuando se ha establecido un beneficio de costo estratégico. Al mismo tiempo, las actividades de mantenimiento de menor valor pueden identificarse y eliminarse a favor de una ejecución adecuada a escala o enfoques de mantenimiento programado más limitados."
"El Mantenimiento Centrado en Confiabilidad (RCM) es un proceso de mantenimiento personalizado determinado a través del análisis de modos de falla potenciales y su impacto en el rendimiento del sistema. Iniciado por la industria de las aerolíneas, el mantenimiento centrado en la confiabilidad abarca el mantenimiento reactivo, preventivo y predictivo (basado en la condición), así como los procesos de búsqueda de fallas para detectar modos de falla ocultos o latentes. Al estudiar las relaciones de causa y efecto junto con la probabilidad y el resultado de cada falla, las tareas de mantenimiento pueden priorizarse de manera rentable en función de la seguridad y la importancia de cada activo para la operación general."
Beneficios:
La implementación exitosa de RCM puede conducir a una mejora en el rendimiento general de los costos, menor tiempo de inactividad y una mayor comprensión del perfil de riesgo general de la organización. Al implementar un método coherente y estructurado para decidir si se deben usar estrategias predictivas, preventivas o de fracaso, el mantenimiento centrado en la confiabilidad puede eliminar las conjeturas y el debate de estas decisiones importantes. Con una perspectiva organizacional de alto nivel, a menudo se pueden evitar prácticas de mantenimiento derrochadoras del tipo ""cortador de galletas"". Los principios de mantenimiento centrados en la confiabilidad también se pueden usar para extender la vida útil del equipo basando las decisiones de reemplazo en la condición del equipo en lugar de los ciclos de vida predeterminados. A medida que se eviten más fallas, los gastos operativos se beneficiarán de reparaciones reducidas, revisiones y tiempos de inactividad. La seguridad y la protección son las consideraciones más importantes de RCM, por lo que se evitan daños a la propiedad y / o al medio ambiente mientras se mejora la participación y la satisfacción de los empleados. El mantenimiento centrado en la confiabilidad es potencialmente la estrategia de mantenimiento general más eficiente porque los procesos de mantenimiento más complejos solo se aplican cuando se ha establecido un beneficio de costo estratégico. Al mismo tiempo, las actividades de mantenimiento de menor valor pueden identificarse y eliminarse a favor de una ejecución adecuada a escala o enfoques de mantenimiento programado más limitados."
Definición:
"El mantenimiento predictivo es una metodología o, en otras palabras, una filosofía corporativa que tiene en cuenta el estado del equipo de una empresa. El mantenimiento predictivo monitorea periódicamente los equipos en función del análisis de los datos recopilados a través del monitoreo o las inspecciones in situ. Uno de los objetivos del mantenimiento predictivo es la verificación oportuna de los equipos con el fin de anticipar posibles problemas que pueden conducir a mayores costos con el mantenimiento correctivo. Sin embargo, el objetivo principal es optimizar el uso de máquinas y equipos, aumentar la productividad y reducir los costos para las empresas. El mantenimiento predictivo es una práctica valiosa para construir un programa integral de gestión de mantenimiento para una planta industrial, pero no reemplaza por completo a los métodos de gestión de mantenimiento más tradicionales. Mientras que los programas tradicionales dependen de las rutinas de servicio para todos los equipos y una respuesta rápida a fallas inesperadas, el mantenimiento predictivo programa tareas de mantenimiento específicas solo cuando realmente se necesitan. No elimina por completo todos los aspectos de los programas tradicionales de mantenimiento preventivo y correctivo, pero puede reducir la cantidad de fallas inesperadas, así como proporcionar una herramienta de programación más confiable para las tareas de mantenimiento preventivo de rutina. Al tener una fusión con la metodología DMAIC, se convierte en una herramienta poderosa ya que evalúa las variables que sistemáticamente tienen las máquinas y las evalúa en su conjunto.
Beneficios:
"El mantenimiento predictivo es una metodología o, en otras palabras, una filosofía corporativa que tiene en cuenta el estado del equipo de una empresa. El mantenimiento predictivo monitorea periódicamente los equipos en función del análisis de los datos recopilados a través del monitoreo o las inspecciones in situ. Uno de los objetivos del mantenimiento predictivo es la verificación oportuna de los equipos con el fin de anticipar posibles problemas que pueden conducir a mayores costos con el mantenimiento correctivo. Sin embargo, el objetivo principal es optimizar el uso de máquinas y equipos, aumentar la productividad y reducir los costos para las empresas. El mantenimiento predictivo es una práctica valiosa para construir un programa integral de gestión de mantenimiento para una planta industrial, pero no reemplaza por completo a los métodos de gestión de mantenimiento más tradicionales. Mientras que los programas tradicionales dependen de las rutinas de servicio para todos los equipos y una respuesta rápida a fallas inesperadas, el mantenimiento predictivo programa tareas de mantenimiento específicas solo cuando realmente se necesitan. No elimina por completo todos los aspectos de los programas tradicionales de mantenimiento preventivo y correctivo, pero puede reducir la cantidad de fallas inesperadas, así como proporcionar una herramienta de programación más confiable para las tareas de mantenimiento preventivo de rutina. Al tener una fusión con la metodología DMAIC, se convierte en una herramienta poderosa ya que evalúa las variables que sistemáticamente tienen las máquinas y las evalúa en su conjunto.
Beneficios:
- Reduce el costo de mantenimiento
- Reduce las averías de las máquinas
- Reduce los paros para realizar reparaciones
- Se reduce el stock de refacciones
- Se incrementa el ciclo de vida de los componentes de la maquinaria
- Se incrementa por lo tanto la producción ya que se puede ocupar efectivamente la capacidad instalada
- Mejora la operación segura de las maquinas
- Se realiza una verificación de las reparaciones
- Utilidades generales en la organización se ven incrementadas